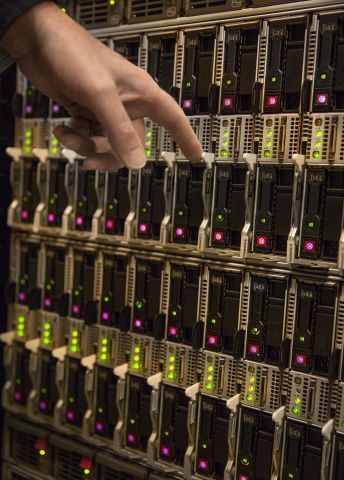
Project Grant 2015
Atomistic Design of Catalysts
Principal investigator:
Magnus Skoglundh, Professor of Catalysis
Co-investigators:
Chalmers University of Technology
Per-Anders Carlsson
Henrik Grönbeck
Anders Hellman
Lund University
Edvin Lundgren
Johan Gustafson
MAX IV
Olivier Balmes
Konstantin Klementiev
Katarina Norén
Institution:
Chalmers University of Technology
Grant in SEK:
SEK 33.5 million over five years
“Imagine if farmers could have their own little factory where they made fuel from the organic waste produced on the farm. They could refuel their own machines and get rid of greenhouse gases at the same time,” says Henrik Grönbeck at the Division of Chemical Physics, Chalmers University of Technology.
He belongs to a team of researchers from four research groups at two Swedish universities who are working together to turn this vision into reality. And the key to success will be a completely new way of manufacturing catalysts.
A dream reaction for catalysis researchers
The farmer in Grönbeck’s example wants to make methanol fuel from methane. Methane is the main constituent of all natural gas, but is also formed when ruminants digest their food. At present methanol is made from methane in large factories. It is a multistep process, which requires catalysts, as well as high temperatures and high pressure. If there were a catalyst that could be used to drive the process in a single step, at normal pressure and lower temperatures, much less energy and space would be required.
“This kind of short-cut would be a dream reaction for people working in the field of catalysis. But it’s an enormous challenge,” says Magnus Skoglundh.
He is Professor of Catalysis at Chalmers’ Division of Applied Chemistry, and is coordinating the project team, whose members also work at Lund University and the MAX IV research facility.
Challenge to finish on time
There are several kinds of catalysis. Heterogeneous catalysis is the commonest industrial form, one in which the catalyst and the reactants have different forms. Usually, the catalyst is a solid on a surface, whereas the reactants are in liquid or gaseous form.
The aim of this new project, funded by the Knut and Alice Wallenberg Foundation, is to make catalysts by deciding exactly where certain atoms are to be placed, so they are positioned optimally in relation to one another. The idea is to make the catalyst selective – to ensure that the only reaction is the desired one. This is particularly difficult in the process converting methane into methanol. The reason is that the same catalysis that turns methane into methanol can cause the methanol to “burn up”, resulting in carbon dioxide and water, instead of methanol.
But if catalysis takes place at fixed points, where a methanol molecule fits like a key in a keyhole, the only reaction will be the first-stage reaction, i.e. the one the researchers want.
“There are enzymes in nature that can do this, for instance bacteria in hot springs,” comments Professor Skoglundh.
The researchers are not basing their approach on flat surface, but rather on three-dimensional structures – crystals known as zeolites, which occur naturally, and can also be synthesized. Metal atoms are dispersed in the zeolites, and serve as the starting point for the catalysis.
Recent science the key to the project
The basic idea does not sound too complicated, but the method is only possible thanks to recent scientific progress.
“We need sufficiently accurate computation methods to thoroughly analyze how the catalysts will work, even before we have made them. Methods have developed rapidly over the past 10-15 years,” Grönbeck explains.
Enormous computational capacity is also needed, something that only a handful of Swedish supercomputers can currently offer. The catalytic reactions can be analyzed at the brand-new MAX IV materials research facility in Lund with the help of synchrotron light – while they are actually happening. The researchers can then make even more computations of how the material can be improved.
“If we succeed, we will have a completely new method of designing catalysts in a few years, and the whole field of catalysis research will benefit enormously as a result. Selective catalysis would make many processes more effective and more energy-efficient,” Skoglundh adds.
Aside from making methanol from methane, selective catalysis could be used in diesel vehicles for direct conversion of nitrogen oxides into pure nitrogen gas, which could be harmlessly released into the air. Another tempting prospect is to manufacture methanol from carbon dioxide. This is already possible, but currently requires high pressure and copious amounts of energy.
“An efficient reaction at normal pressure would be fantastic. It would make use of the carbon dioxide that currently is nothing but a problem,” enthuses Grönbeck.
Text Lisa Kirsebom
Translation Maxwell Arding
Photo Magnus Bergström